Classic Works 與 JLR 總部所在的 Coventry,是集團中豪華轎車品牌 Jaguar 的發源地,第 2 天的行程重點,則是移動到豪華越野品牌 Land Rover 的發源地 Solihull。
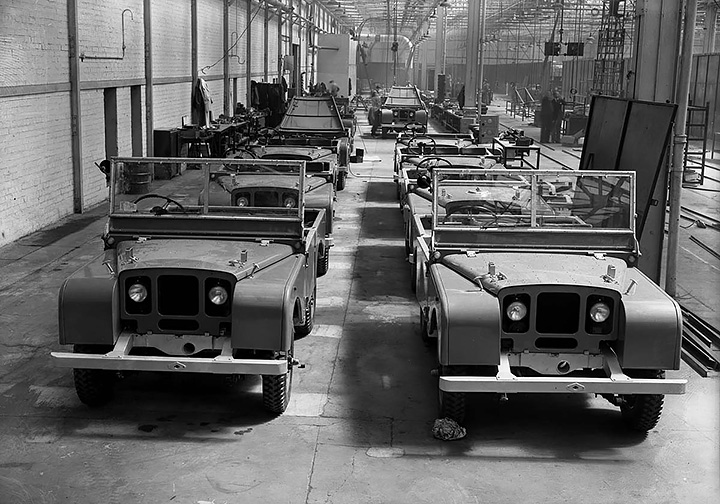
Classic Works 的參訪,是向臺灣媒體展現 Jaguar Land Rover 的光榮歷史。Solihull,則是為了展現 Jaguar Land Rover 獨步全球的鋁合金車體打造技術。Solihull,是目前全球最大的鋁合金車體工廠。
全球汽車產業的鋁合金專家,推廣鋁合金科技不遺餘力
Jaguar Land Rover 是全球汽車產業中的鋁合金車體專家,不僅如此,Jaguar Land Rover 還是全球汽車產業中鋁合金技術的傳教士。Jaguar Land Rover 不僅持續投入鋁合金的研發生產,還歡迎全球汽車產業到廠參觀,與大家分享鋁合金製造的技術與知識,推動業界對於鋁合金材料及生產器具的共同標準,期望能在汽車業界推廣鋁合金材料的運用。包含 Mercedes-Benz、Audi、Ford 等品牌,都曾派人到 Solihull 廠區來參觀交流。
鋁合金質輕剛性強,是受歡的環保材質
鋁合金質地輕、剛性高,是許多性能取向的產品上所愛用的材料。而鋁合金因為化學特性的緣故,氧化層十分緻密,並不像鋼材那般鬆散,因此車體不易出現鏽蝕的問題,也讓鋁材的回收再生率遠遠高於鋼材,環保表現十分優異。Jaguar 早在 1940 年代的 XK 120 就已經採用鋁合金鈑件,而衍生的 Le Mans 冠軍車 C-Type、D-Type,亦均是大量使用鋁合金材料所打造;而在 1948 年所發表的 Land Rover Series I,其充滿鉚釘的獨特車體,亦是由鋁合金所打造。Jaguar Land Rover 與鋁合金的淵源,早已超過 70 年。
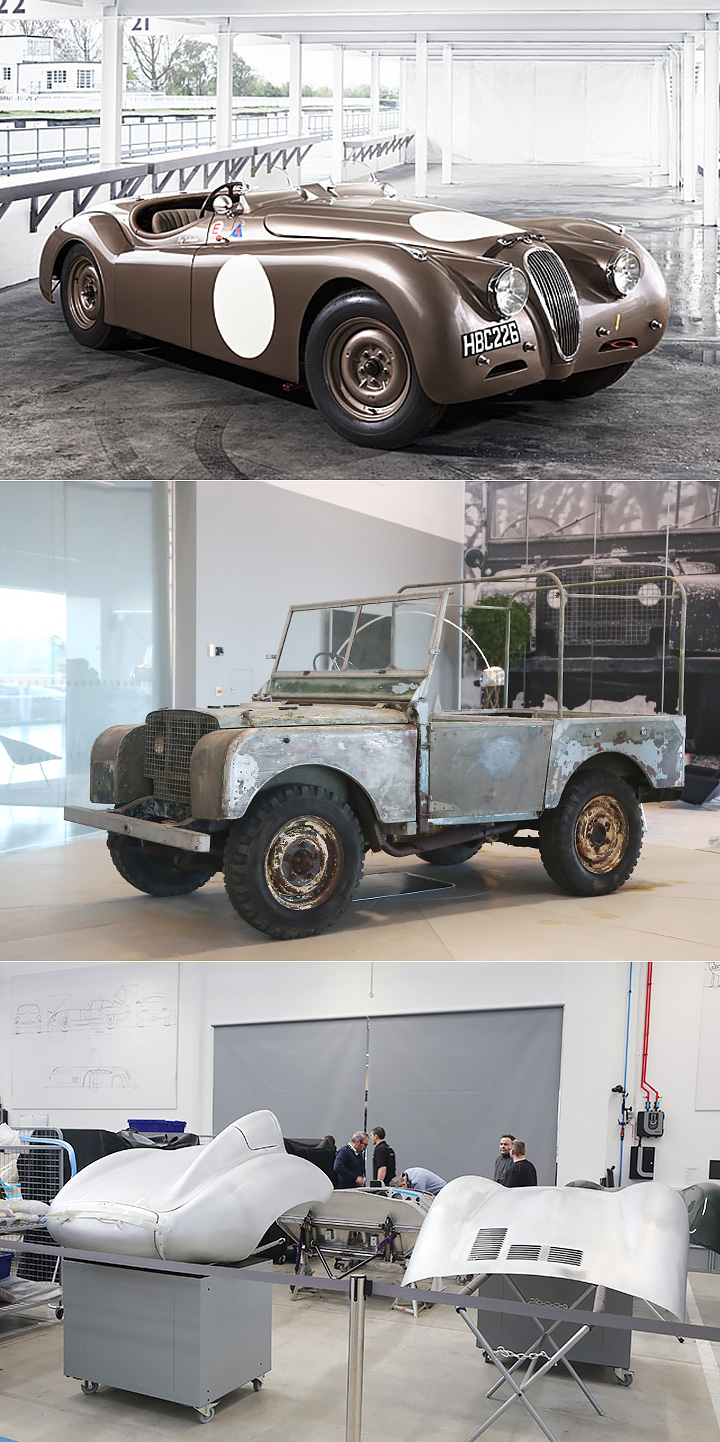
然而,鋁合金的機械性質與鋼鐵不同,讓其在加工使用上不如傳統鋼鐵材料來得方便,加上提煉成本高,讓鋁材的價格居高不下,使得量販車款仍是以鋼材做為主要的材料。
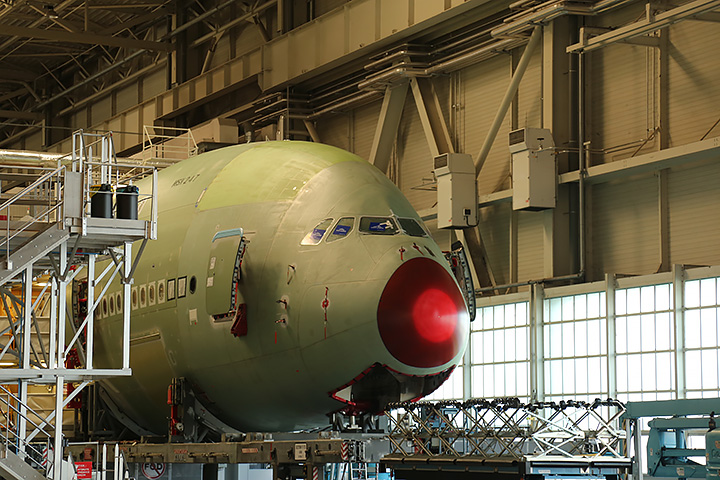
21 世紀環保意識高漲,鋁合金行情看俏
隨著時間進入 21 世紀,汽車產品的設計持續的放大,消費者對於性能與動力的要求不斷扶搖直上,而環保意識的擡頭,亦讓油耗、排放的規範變得極為嚴格。在這樣的環境之下,鋁合金材料再次受到汽車產業的重視。Jaguar 在 2003 年推出第 7 代 XJ 時,便以全鋁合金打造這世代的旗艦產品,讓其在高剛性的表現之後,同時有輕盈的車重,搭配強勁的動力,在絕佳的舒適性同時,提供卓越的運動性能。
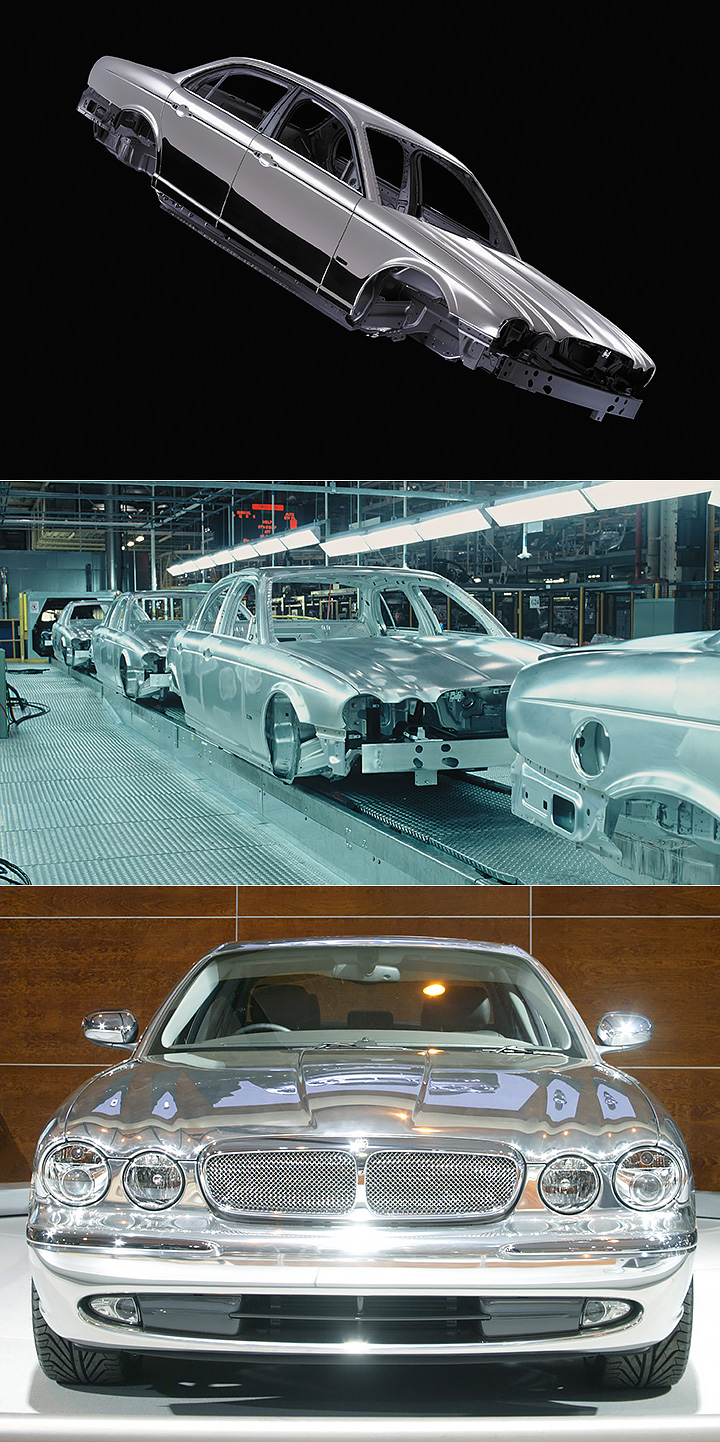
不僅是 Jaguar,同一集團的 Range Rover 亦在 2012 年所推出的第 4 代 Range Rover,以全鋁合金打造這輛新世代旗艦產品,為其一口氣減輕了 420 公斤的車重。自此以往,Jaguar Land Rover 便不斷將旗下車款改以鋁合金車體所打造,以達到環保、節能、永續的目標。
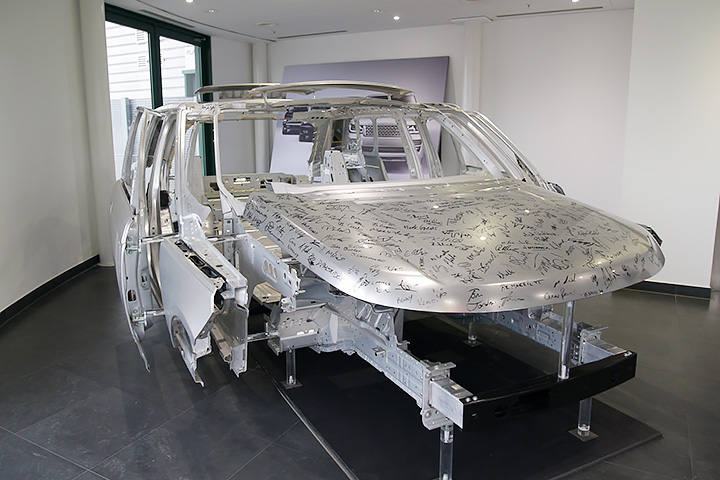
目前 Jaguar 旗下的 XJ、F-Type 及 Land Rover 旗下的 Range Rover、Range Rover Sport 等車款,均是採全鋁合金車體設計,而包含 XF、XE、F-Pace、Discovery 等車款,鋁合金的比例亦超過 7 成,讓 Jaguar 及 Land Rover 的車款,在保有豪華大氣的車格之外,依舊能保持輕盈的車重,在性能、油耗、排放以及回收再利用上,擁有絕佳的表現。
佔地超過 300 英畝,Jaguar Land Rover 最大生產基地
Solihull 廠區佔地超過 300 英畝,也就是超過 1.2 平方公里,或是超過 123 甲,佔地十分廣大,是 Jaguar Land Rover 旗下最大的生產基地。Jaguar Land Rover 在此設置了鋁合金衝壓廠、3 個車體組裝廠、塗裝廠、2 條最終組裝線,包含 Land Rover 的 Range Rover 短軸/長軸、Range Rover Sport、Discovery 以及最新的 Range Rover Velar,以及 Jaguar 的 F-Pace 均是在此生產。
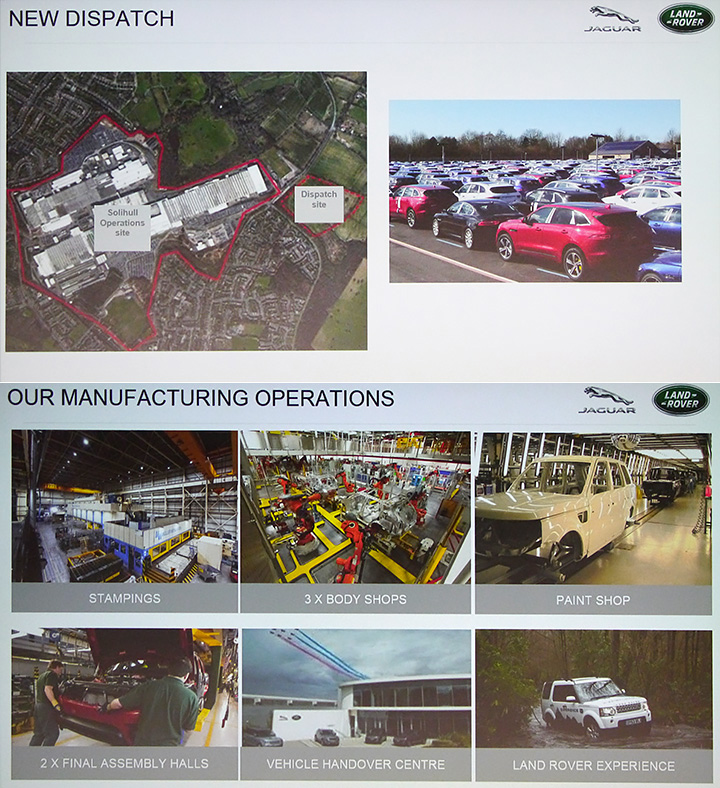
因應全球市場對於新世代產品需求的快速成長, Jaguar Land Rover 在過去數年間,總共投入了 15 億英鎊,總合新臺幣 600 億元的投資,進行生產設計的改進,讓這個廠區,擁有全世界最先進的鋁合金車體打造技術。讓廠區僱用的人員變成原本的 2 倍,光是負責物流的人員就高達 3,500 人,總員工人數更高過 1 萬人,而車輛的產出更是變成 3 倍,每天可以送出 1,800 輛新車,以送至全球各地的車主手中。
為達成如此高的產量,在這個廠區中,每小時有超過 1,000 輛的貨運車輛,從各地的供應商,帶來各種不同的零部件,以因應生產組裝線的需求。每天從各地湧入的零件高達 1,350 萬項。因此廠區內隨時可見大型的貨運車輛穿梭往來,十分忙碌。
而臺灣媒體受邀參訪的,便是 Solihull 引以為傲的自動化車體組裝廠以及 Range Rover Velar 與 Jaguar F-Pace 的最終組裝線。而與眾多汽車公司的組裝廠參觀不同,Jaguar Land Rover 全程開放媒體拍攝,就讓小亮以第一手帶回的影片,帶著大家一同參觀這座全球最先進的鋁合金汽車工廠。
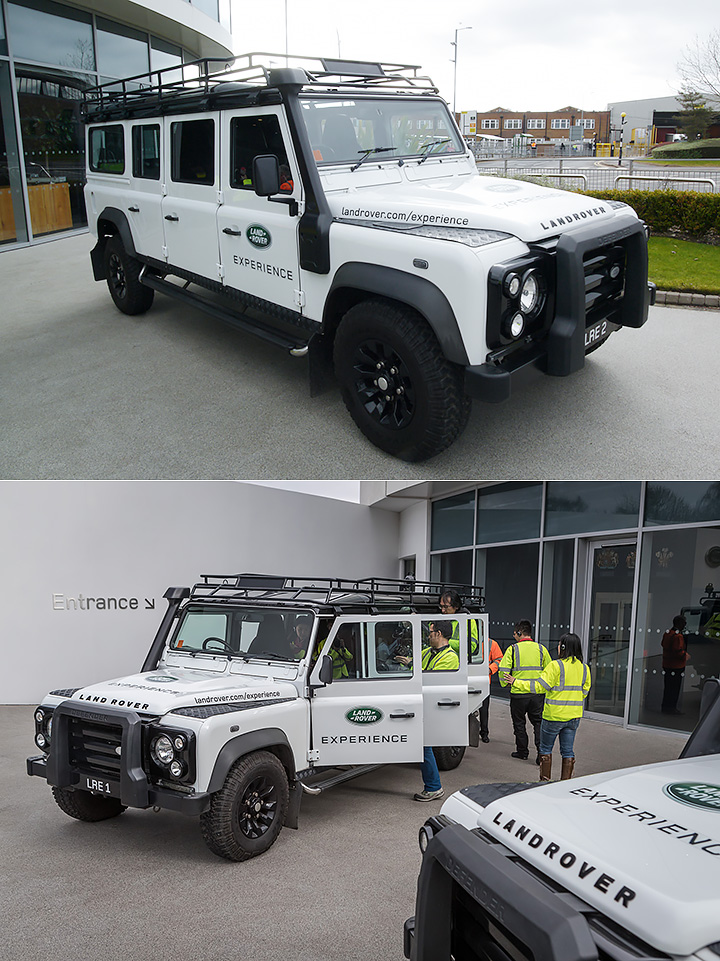
耗資 15 億英鎊升級至最新自動化生產線
在巨大單一廠房,可以看到超過 700 具的機械手臂森然羅列,規律而快速地在進行組裝,這是 Jaguar Land Rover 的最新的自動化鋁合金車體組裝廠。在這個自動化的車體組裝廠中,在最高速運行之下,每 76 秒可以產出 1 具車體,再透過輸送帶,送往塗裝烤漆後,再送至組裝線,與引擎、傳動系統、電系、內裝等零部件組裝,變成成車,再通過品質檢測程序之後,成為一輛輛的成車,送至全球各市場的買家。
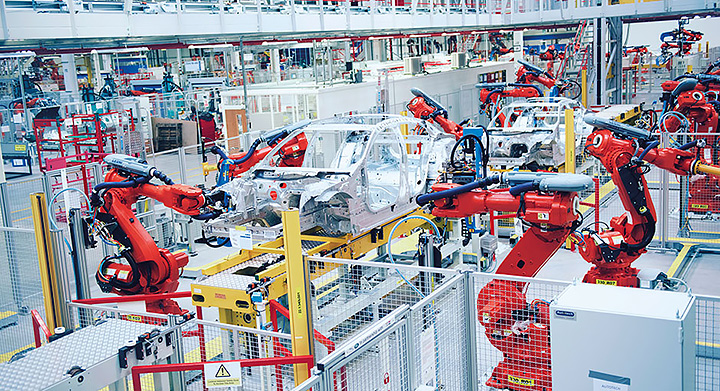
參觀工廠對於小亮而言並不是新鮮事,但是鋁合金車體組裝廠卻是第一遭。與傳統鋼製車體廠不同,Solihull 的車體組裝廠,很明顯少了金屬點焊的氣味以及到處噴灑的火花,讓整個參觀的過程之中,空氣顯得十分的清新。
一如本文一開頭所提到,鋁合金在物理特性上與鋼鐵材料不同,焊接處理較為麻煩,因此現在現在鋁合金車體的組裝上,多與航空產業相同,採用膠合鉚接的方式進行,因此現場的機械手臂,並不像傳統車體廠內多為點焊的需求,而是上膠以及鉚接的特製機械人,在生產上有所不同。
只見機械手臂群中間,由輸送帶送來甫上膠預組的車體,多支機械手臂便會按著程式設計,移動到責任區域,開始進行鉚接的工作,相較於傳統的火花四散的點焊生產線,Jaguar Land Rover 的機械人安靜許多。
影片中可以看到車體內部結構在預組立之後,輸送至本工作站,由機械手臂進行鉚接的動作,以完成組裝。
此工作站負責的工序,是組合車體的內部組構與外部鈑件。
當前 1 個車體完成此工作站的工序,要送至下一個工作站時,畫面右方機械手臂先回到準備位置,並更換鈑件吸持器,以為下一個車體工序進行準備。
當下一個車體來到工作站時,機器手臂把放置在左側的鈑件吸持至車體旁,等待工作站另一側的鈑件。而另一側的鈑件正由另一組機械手臂進行上膠動作,上完膠之後,吸持至本工作站的放置區,再機械手臂同步擺放至定位,進行組裝。
在裝上外部鈑件的車體,則是送至此工作站,進行鉚接固定的工序。
在小區塊組裝的部份,為了節省場地空間,Jaguar Land Rover 還設計了直立的輪式組裝臺,在輪鼓的一側,有 1 組機械人負責將不同的鈑件安置至夾具上,並上膠,做成預組立,而除著輪鼓旋轉至另一側,則有另 1 組專責的機械人進行鉚接的工作,讓鈑件之間牢牢固定,以便送至後續組裝線,完成車體的組立。
這個直立式輪式組裝臺,是用來進行車體內部結構組件裝配之用。由於組件體積較小,因此將治具夾具安裝在輪式組裝臺上,可以減少使用的空間。畫面左邊的機械手臂持續在進行組件鉚接的工作,畫面右側的機械手臂則在將最基本的結構件放置至定位,並進行上膠的工序。
而在各工作站都可以看到,1 道工序完成,工件被送往下一個工作站以進行下一道工序之時,各機械手臂亦會回到準備位置,進行不同鉚接夾頭的更換,或是鉚釘零件的裝載,以為下一組工作的到來做準備。
由於高度的自動化,這個最新的鋁合金車體工廠,僅需要 125 名工作人員便可以持續地運作,是目前全球技術領先的鋁合金車體工廠。
全球最大的鋁合金鈑件,重量僅有 7 公斤
要了解鋁合金的優劫,2012 年開始生產的第 4 代 Range Rover 正是最好的例證。Range Rover 車側的結構鈑件,從頭到尾是一體化的設計,是當時世界上最長的鋁合金鈑件,是 Jaguar Land Rover 鋁合金生產工藝的代表。而令人訝異的是,這塊全球最大的鋁合金鈑件,在提供高強度的表現之下,僅有 7 公斤的重量,這也難怪 Range Rover 較第 3 代產品減輕超過 400 公斤之多。
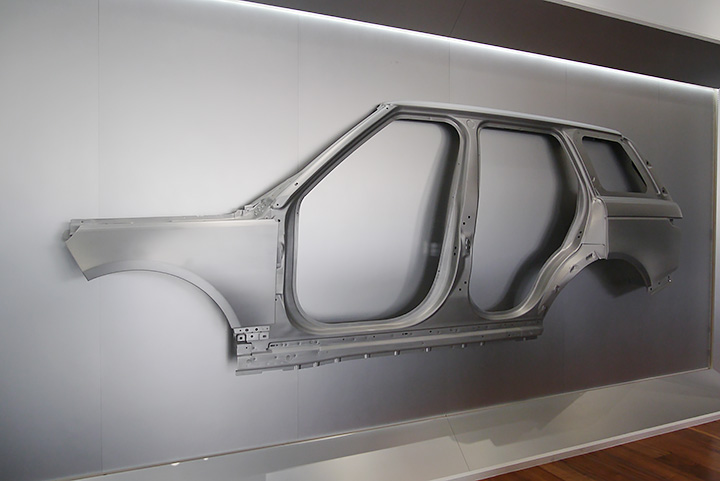
此外,原廠人員亦特別介紹,Range Rover 等高階車款,在大面積鈑件之間產生的腔室,會造成諧振與回響,在行車的靜肅性上有所減損,因此 Jaguar Land Rover 的工程人員特別進行聲學的檢查,在適當的地方加上一塊塊的隔離器,其外側的黃色發泡材料在烤漆時會受高溫而膨脹,截斷腔室,並吸收振動與噪音,確保行車的靜肅表現。
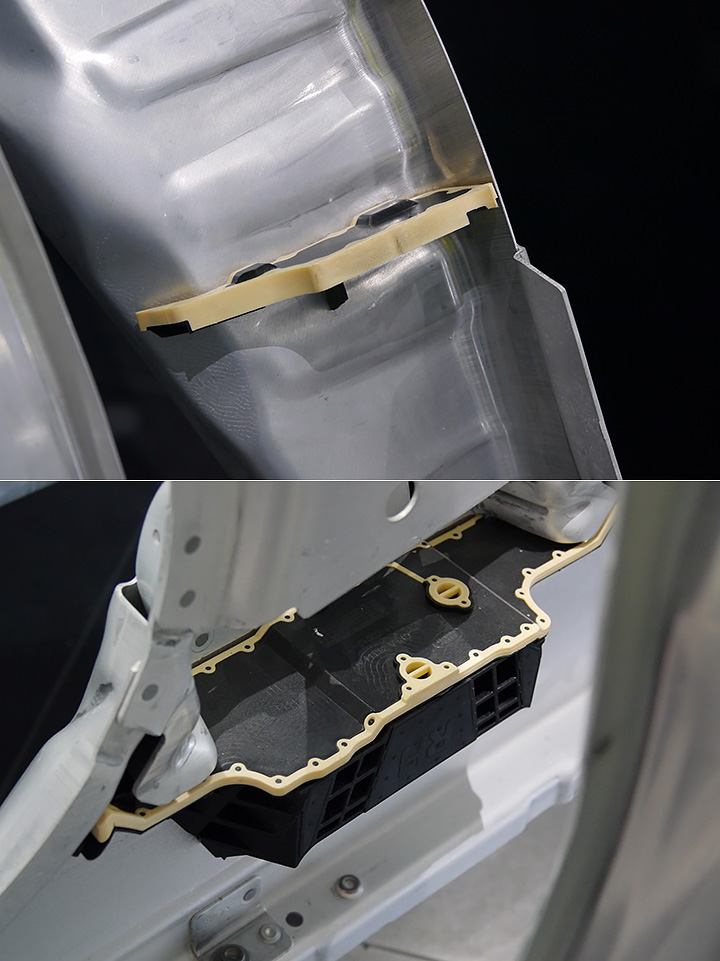
而在這個工廠完成的車體,Jaguar Land Rover 便會以輸送帶送至塗裝廠,經過化學清洗、鍍鋅塗布、靜電塗裝、烤漆、檢查之後,嶄新亮麗的車體,再次送了輸送帶,送到最終組裝廠,以進行最後的步驟。
最後組裝線
相對於鋁合金車體廠,Solihull 的最終組裝線與其他品牌的最終組裝組的差異就沒那麼大,然而 Jaguar Land Rover 在近期的投資中亦進行了更新,可以看到組裝線的工具及輔具均是新式設計,能有效協裝組裝工作,減輕工作傷害。
為求全車烤漆色澤的一致,現代的汽車車體均是全車一起送至塗裝烤漆廠以獲得最佳的效果。然而為了避免在後續安裝過程之中發生擦碰傷及漆面,在進入最終組裝廠後,工作人員會先把車門卸下,以便進出車室工作,及進行車門零件的安裝,並為高風險區域加上防護墊,以保護漆面。然而車體與車門將會由不同的輸送帶進行輸送,送至不同的組裝線,以提高組裝的效率。
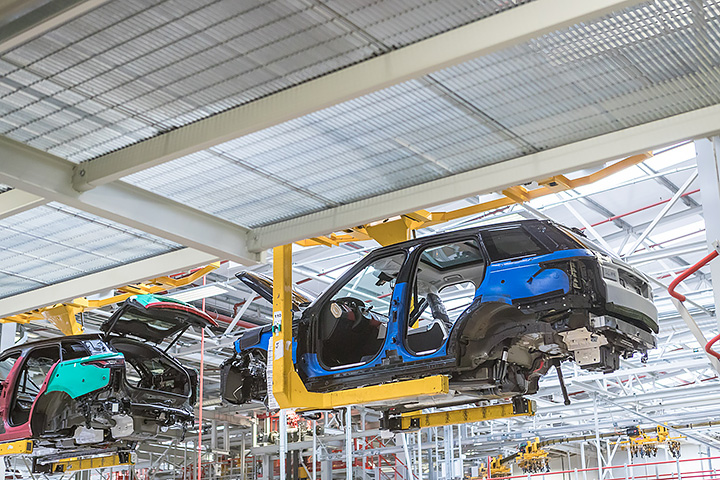
在現代的汽車組裝中,由於大多是採單體式車身,因此懸吊系統與引擎、變速箱、傳動系統等,均是由另一條組裝線進行組裝。隨著工作臺在輸送帶上前進,作業人員依序分工裝上不同的部件。影片中則是底盤組裝線最後的品質檢測部份。由於採混線生產,可以看到各工作臺上的引擎、變速箱、懸吊組的差異相當地大。
組裝好的車體與組裝好的動力系統,在這個工作站進行結合。在汽車產業中,以 Marriage 稱呼這道工序。在車體與底盤結合之後,系統會自動為車輛同步上緊螺栓,此時車輛已經十分接近成車。
在現代化的最終組裝廠中,輸送帶的設計十分複雜,會依空間需求,飛天遁地,也會從軌道吊車轉移至平面輸送帶,加上各種不同輸送帶之間的同步,是極為專業的工程領域。
在內裝也安裝完成後,車輛送至這個半密封的工作站,添加油液,準備上路。
從車體拆下的車門,以獨立的輸送帶送至組裝線,以進行電動裝、喇叭、門鎖、飾板的安裝。
當車輛離開油液添加區,獨立運送的車門亦在電腦精準的控制下,來到工作站,與久違的車體結合。
在車門重新組裝之後,組裝線人員會進行最後的細部安裝,1 輛全新的產品就可以準備下線了。而 Jaguar Land Rover 在此最後的階段,在每一個工作臺旁安裝有黃色的電腦,能在最後階段為車輛充電,同時進行檢測,以確保車輛的系統均正常運作。
開放參觀,線上報名
在參觀之後,Jaguar Land Rover 在鋁合金車體技術上的投入讓人印象深刻。而事實上,Jaguar Land Rover 亦提供付費導覽行程,開放一般消費者參觀。有興趣的朋友,可以透過 Jaguar Land Rover 的網站預約,便能與小亮一樣,親眼見證這全球領先的汽車科技。
原廠網址:
https://experience.landrover.com/manufacturing-tours/manufacturing-tour-solihull
費用:
成人每人 49 英鎊
兒童每人 39 英鎊
注意事項:
10 歲以上,未滿 16 歲須有成人陪伴。
討論區
成為第一個發表的人